Due to Liquid Helium’s (LHe) extremely low temperature and high production cost, Barber-Nichols (BN) specializes in liquid helium pumps that minimize heat input. Specifically, these pumps utilize a long pump shaft and a vacuum housing to satisfy this requirement while providing long, reliable life, and ease of maintenance. The liquid helium pumps show the vacuum housing in place (top) and the vacuum housing removed (bottom). These pumps circulate liquid helium that cools toroidal magnets in CERN’s ATLAS Experiment. The anti-convection/radiation shields and engineered inducer for low Net Positive Suction Head (NPSH) can be seen on the pump with the vacuum housing removed.
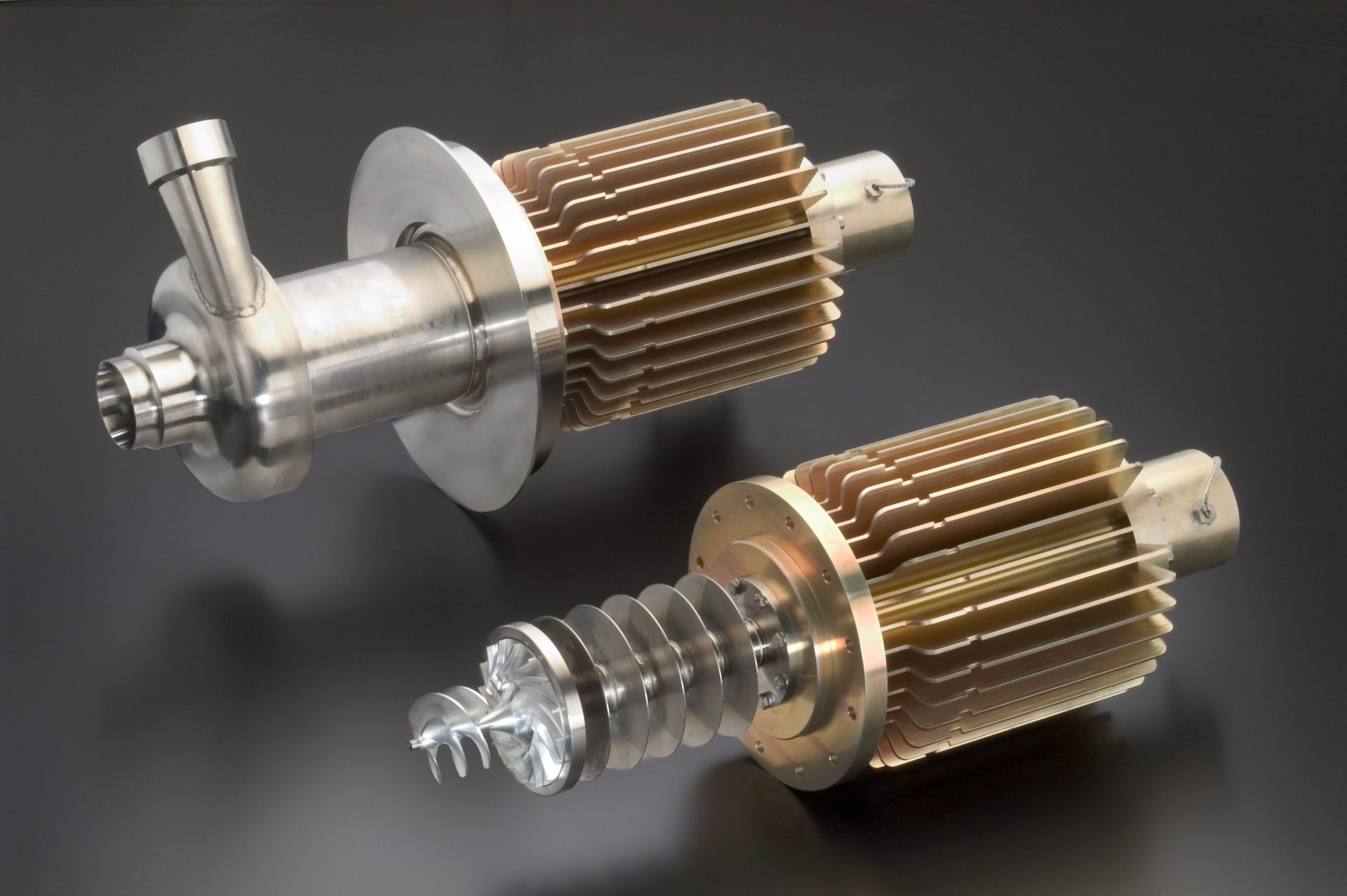
Liquid Helium Pumps
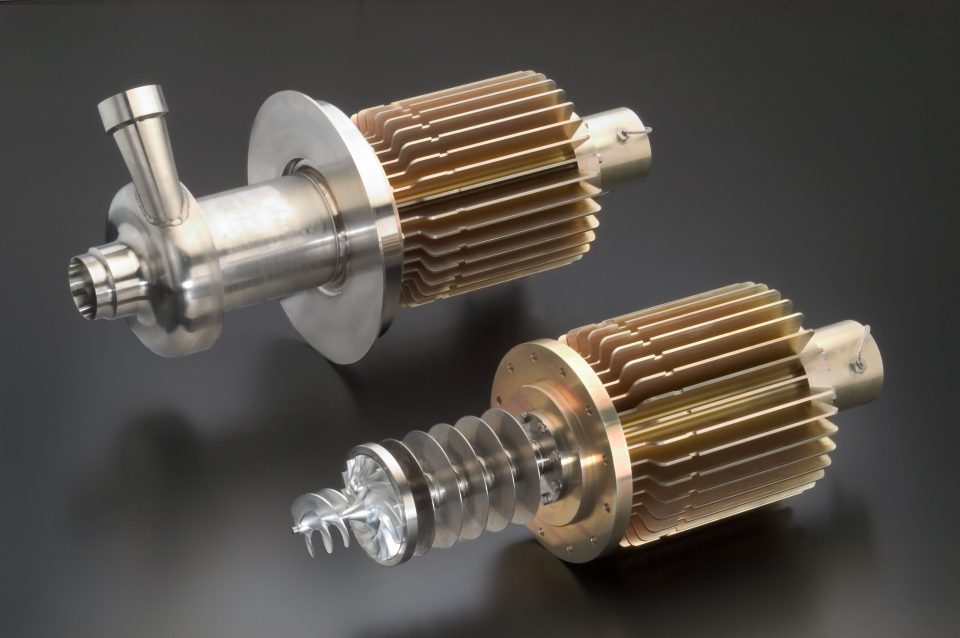
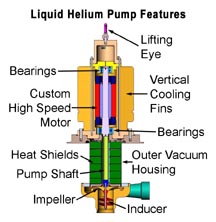
Liquid Helium Pump Features
- Anti-convection/radiation heat shields minimize heat input to the cryogenic fluid by disrupting natural convection currents and creating barriers to radiated heat.
- A long, thin-walled pump shaft and outer vacuum housings minimize heat conduction into the cryogen.
- High-speed operation and the use of variable frequency drives increase hydraulic efficiency and minimizes generated heat.
- Vacuum housings allow pumps to be removed from a system for regular maintenance without breaking the cold box vacuum. This reduces time and preserves the system integrity during routine maintenance.
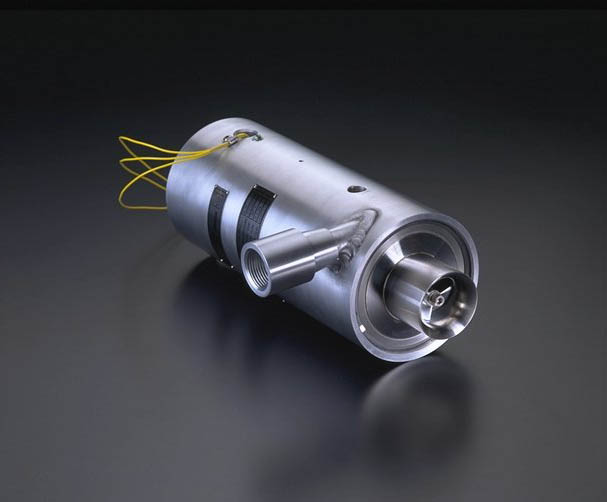
In some low-power helium applications, it is advantageous to use a submersible pump. Submersible liquid helium pumps eliminate continuous heat input because the entire pump operates at LHe temperatures. Additionally, the motor is extremely efficient at cryogenic temperatures and a very small percentage of total power is transferred to the helium due to motor inefficiency, windage, and bearing losses. BN has developed submersible pumps for liquid helium that use AC induction and brushless DC motors. Submersible liquid helium pumps are typically used for fluid destratification and aerospace transfer or recirculation. These compact, economical pumps endure thousands of start/stop cycles and provide many years of maintenance-free operation.
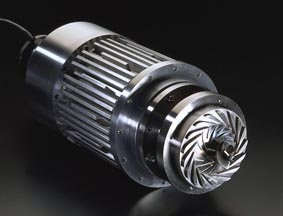
Case Study
BN was contracted on a NASA phase II SBIR to design and build a liquid helium pump with variable impeller blade heights to maximize its performance range. In this successful program, the pump was designed, produced, and tested at BN. By changing the impeller blade height along with varying the speed, the pump was capable of operating over a complete head and flow range up to the pump’s maximum speed.